How Inventory Batch Pre-Processing works
Author:
Fluent Commerce
Changed on:
12 Feb 2025
Overview
This document outlines the functionality of Batch Pre-Processing, offering insights into how unchanged records are filtered during the ingestion using Batches.
Key points
- Efficient Processing: Inventory Batch Pre-Processing handles batch inventory updates before they reach the inventory workflows, streamlining the process.
- Change Detection: Identifying inventory records that have changed, ensuring the workflow engine processes only necessary updates.
- Performance Improvement: Reduces workflow engine load by filtering unchanged records, enabling faster and more efficient inventory processing.
- Enhanced Flexibility: Supports additional fields in batch records, allowing for more precise control and management of inventory updates.
Pre-requisites
- You should have knowledge of Global Inventory
- Understand the overview of Inventory Batch Pre-Processing
- You have an understanding of the Workflow Engine
Architecture
Overview
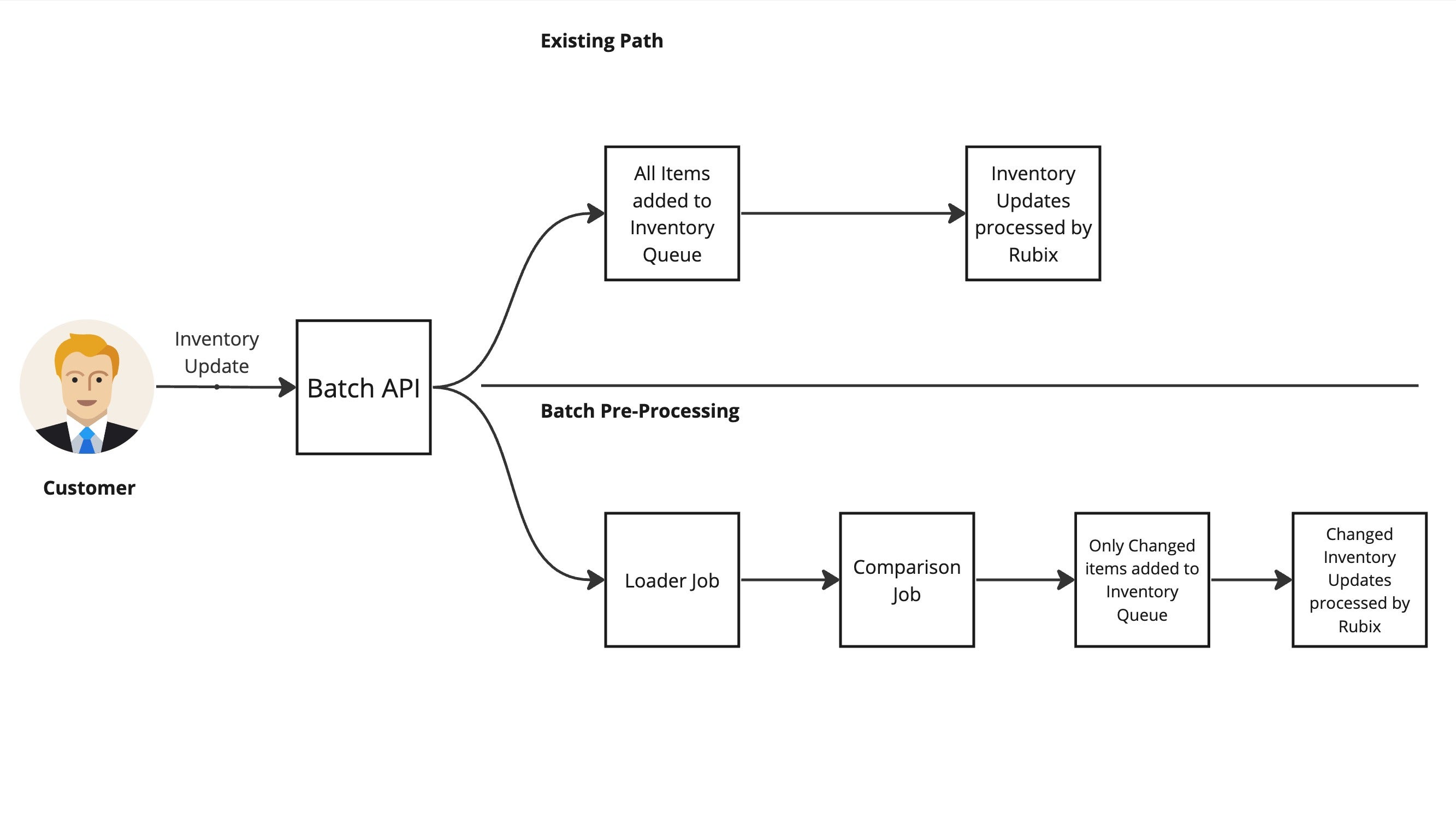
In traditional update processes, batch updates are split into individual records and added directly to the Queue for processing. This can be inefficient, especially when many records haven't changed and don't require processing.
Batch Pre-Processing introduces a more efficient flow:
- Initial Analysis: Instead of immediately processing each record, the system first analyzes the batch to identify which records have actually changed.
- Selective Processing: The workflow engine forwards only the records identified as changed to the Inventory Queue for processing.
- Optimized Workflow: This reduces unnecessary workload on the workflow engine, improving overall system performance and reducing processing time.
Components
The Batch Pre-Processing system consists of two main components:
1. Loader Job
Purpose:
The Loader Job loads existing data from the database. This includes current quantities, statuses, and any active transient quantities.
Function:
- Data Gathering: Collects the current state of inventory positions and quantities.
- Preparation for Comparison: Prepares data for the Comparison Job to use in determining changes.
2. Comparison Job
Purpose: The Comparison Job compares the new batch updates against the existing data loaded by the Loader Job.
Function:
- Change Detection: Determines whether each inventory update represents a change that needs processing.
- Criteria for Change:
- Inventory Quantity Identification:
- Quantity and Status Comparison:
- Transient Inventory Quantities Check:
Result: Only updates marked as changed are forwarded to the Queue for processing.
Understanding Transient Inventory Quantities
- Definition: Transient inventory quantities are temporary adjustments due to sales, reservations, corrections, or other activities.
- Significance: Their presence indicates recent activity affecting the inventory position, necessitating reprocessing of the update.
Decision Logic Flow
Here's a detailed breakdown of how the Comparison Job decides whether an update is "changed" or "unchanged" for each record in the batches processed for the current preprocessing execution :
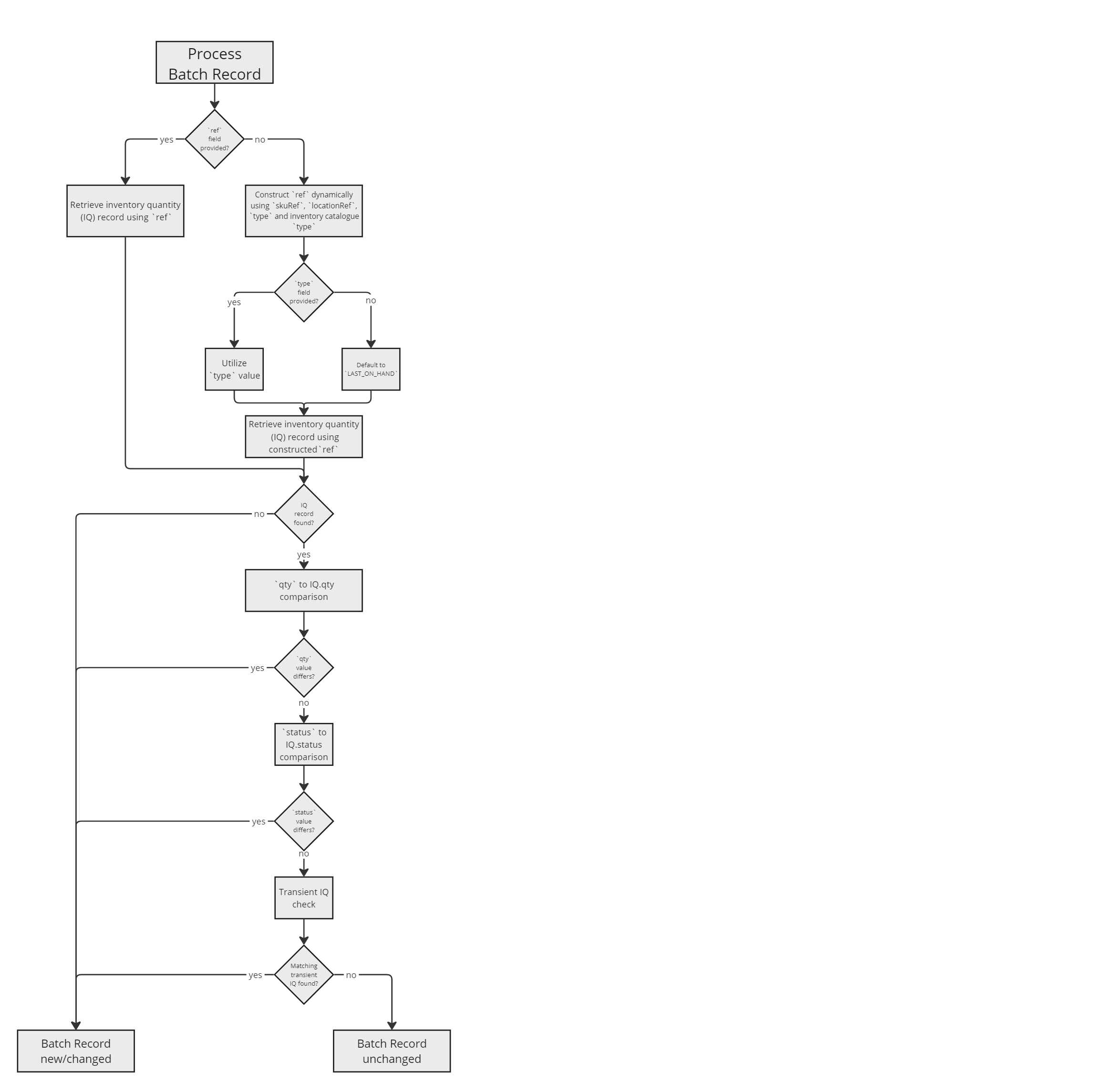